The saga continues with my new-to-me loom. This is a continuation from
Part 1. I can now say that it is warped, but I now wonder about the header. Suggestions are DEFINITELY welcome!
With the warp beamed, I was able to set up the sections of warp through the heddles and reed. There are four warps to the group and I set the two outside into one harness and the inside two to the other.
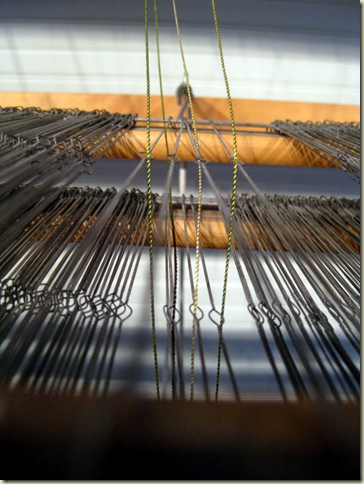
The groupings of warp are 3 inches apart, so I set a tape measure on the reed to tell me if the placement was correct.
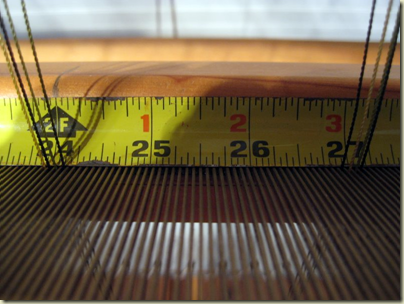
I was rather proud of myself when I finished the last group, until I realized that I had not sent the warp over the castle before heading into the heddles. This is one reason that I’ve chosen this simple warping – mistakes like that are not hours in the undoing!
I tied off to the bottom rod.
Tommye Scanlin has a great tip in tying off the bar to the front of the loom to get the first round of tying off complete.
Here we are over the castle, through the heddles and all the groups checked out for being in the correct harness!

I then inserted 4 of the spacers within the warp and spaced the warp out correctly.

With that you can see here the outside/inside order of the groups and hopefully can imagine what will happen once I start placing the bamboo in there.
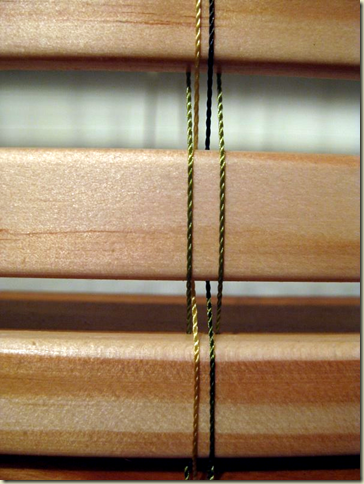
The next step is generally to put in a header and some sort of weft protection (something to keep this from falling apart when I take it off the loom). I’ve thought about tying off a small portion of warp at each group, but wonder what you all think?
Still plugging away at preparing the bamboo, but hopefully I’ve got enough to get started and see where the next roadblock is!
4 comments:
It's great that your warping is progressing.
I have no clue how to help (or you know I would), but I'm sure some later commenter will have a great idea!
Good luck!
Sue
Very interesting!
You might try doing a small weft-faced area (possibly 1/2" worth) for each of the four groups after a little header to get it started. You're right, this is going to be tricky to pull out the beginning slats and keep the first parts of the bamboo contained until you can control it. Maybe consider doing the 1/2" of weft-faced area with the same yarn as your warp, then saturating that with PVA or even Aileen's Tacky Glue. Let it dry, of course, before proceeding. PVA and the Aileen's will both dry clear, I believe, but if you wanted to use maybe sample on some of the warp separately from the loom, let it dry and see what it looks like. Those small areas could then be tucked to the back like tiny hems so that the bottom edge was actually the first bamboo strip.
Just a though! You engineers... you always like to keep people (and yourselves) thinking, don't you!?
Looks interesting. I'm no help with advice Jennifer,
BUT the upside is whatever mistakes or modifications you make on this warp, you'll remember forever and in the case of mistakes probably never repeat. A first warp is a lasting lesson.
For a header to keep the bamboo stalks in place, can you try sewing the bamboo in the closely spaced areas of the warp just enough to secure until you do your end finishes?
Thanks for the encouragement! One of my gifts is lots of ideas and one of the curses is that they are generally out of the realm of the mainstream!!! I just can't do things normally!
Theresa, normally with yarn, I would "sew" on the warp to hold it in. Maybe I need to think like that on a stronger scale - i.e. with the nylon. Thanks!
Tommye - that's a great idea on the weft! I'm familiar with PVA at work and wonder if you are referring to the same thing. Does your PVA dissolve in boiling water? That's an interesting thought to form some fabric as you suggest and stiffen/strengthen it with PVA. Then after all is safely off the loom, I could remove the PVA from one group at a time and finish it with some technique from Collingwood's book. Hmmm... - got to check that out! Thank you!
Post a Comment